Step 1: Designing Smarter, Faster, and Better
Tool: Pelles & Drawer
Read more on their website (Pelles & Drawer)
Description
The design phase is the backbone of every MEP project. This is where creativity meets technical precision, and even minor errors can lead to costly delays or rework. Traditionally, this phase required long hours of manual drafting, estimating, and layout planning. However, Pelles.ai and Drawer AI are changing the game by introducing smarter, faster, and more reliable workflows powered by AI.
These tools focus on addressing the inefficiencies of manual design processes while enhancing accuracy. Whether it’s interpreting incomplete drawings or automating complex electrical layouts, they make the design process seamless and highly efficient.
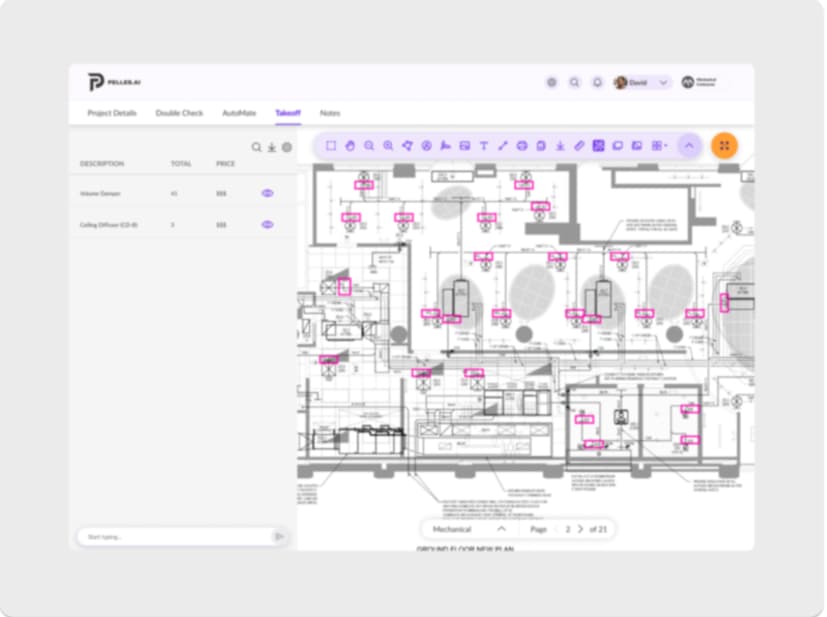
Problems These Tools Solve
- Incomplete or Poorly Detailed Drawings:
Pelles.ai transforms basic single-line diagrams into comprehensive double-line layouts, automatically filling gaps with precision. - Error-Prone Manual Workflows:
Drawer AI reduces manual errors by automating device detection and calculating electrical layouts. - Time-Consuming Processes:
Tasks like estimating pipe lengths, generating feeder layouts, or marking up documents now take minutes instead of hours. - Team Coordination Challenges:
Both tools ensure smooth integration with BIM platforms and other estimating systems, improving collaboration across disciplines.
Features and Unique Use Cases
- Automated Design Generation
- Pelles.ai: Automates preconstruction activities like takeoffs, document markups, and layout generation.
- Drawer AI: Detects devices in PDF drawings, quantifies them, and generates efficient branch and feeder layouts.
- Error Reduction
- AI-driven calculations ensure material quantities are precise, reducing overestimation or missed components.
- Seamless Collaboration
- Outputs integrate with BIM software and estimating tools, ensuring every team member has access to updated, accurate data.
- Real-World Intelligence
- Beyond automation, both tools provide actionable insights, enabling teams to make data-driven decisions faster.
Step 2: Enhancing Collaboration Across Teams
Tool: Trimble SysQue
Read more on their website here
Description
Once your designs are finalized, the next step is to ensure seamless collaboration between all project stakeholders, from engineers to fabricators. Miscommunication, outdated plans, or disjointed workflows can result in costly errors, delays, and inefficiencies. Trimble SysQue tackles these challenges by transforming your Revit models into detailed, real-world designs that are fabrication-ready and accessible to all team members.
Trimble SysQue builds on the foundation of Revit, turning its standard models into comprehensive, constructible designs. It introduces real-world manufacturer-specific components, making every detail precise and actionable. Whether it’s creating spool sheets, laying out hangers, or preparing models for fabrication

Problems It Solves
- Outdated or Incomplete Plans:
Teams often work with incomplete or outdated models, leading to discrepancies and rework. SysQue ensures everyone uses the most current, detailed models. - Team Misalignment:
Gaps between design, detailing, and fabrication can slow down workflows. SysQue bridges these gaps, creating a seamless workflow. - Manual Errors:
Complex tasks like spool creation and hanger layout are automated, significantly reducing the chance of human error. - Inefficient Communication:
SysQue provides a centralized platform that aligns all team members, ensuring clarity and better coordination.
Features and Unique Use Cases
- Access to a Real-World Component Library
- SysQue includes over 8 million manufacturer-specific parts, ensuring models are accurate, constructible, and aligned with real-world products.
- Use these components to create detailed layouts that are ready for fabrication.
- Fabrication-Ready Models (LOD 400)
- Generates highly detailed Level of Detail (LOD) 400 models, bridging the gap between design and physical construction.
- These models allow for direct fabrication, saving time and ensuring accuracy.
- Integrated Hanger and Support Layouts
- Quickly design hangers and supports in your models and export them directly to Trimble Field Link for precise execution on-site.
- This feature is invaluable for ensuring accurate placement and reducing rework.
- Streamlined Estimating and Budget Insights
- SysQue integrates seamlessly with estimating tools, allowing project managers to connect their models to budgets with just one click.
- This improves project visibility, offering better control over costs and timelines.
Step 3: Detecting and Resolving Clashes Before Construction
Tool: Solibri
Read more on their website here
Description
In any MEP project, multiple systems—such as plumbing, HVAC, and electrical wiring—must coexist in the same physical space. If these systems clash, it can lead to costly rework, project delays, and even safety risks. Identifying these conflicts early in the design phase is critical, and Solibri is a tool that makes this process seamless.
Solibri leverages AI to scan BIM models, detect clashes, and validate compliance with building codes. It helps ensure that every design detail aligns with regulations and works harmoniously with other systems.
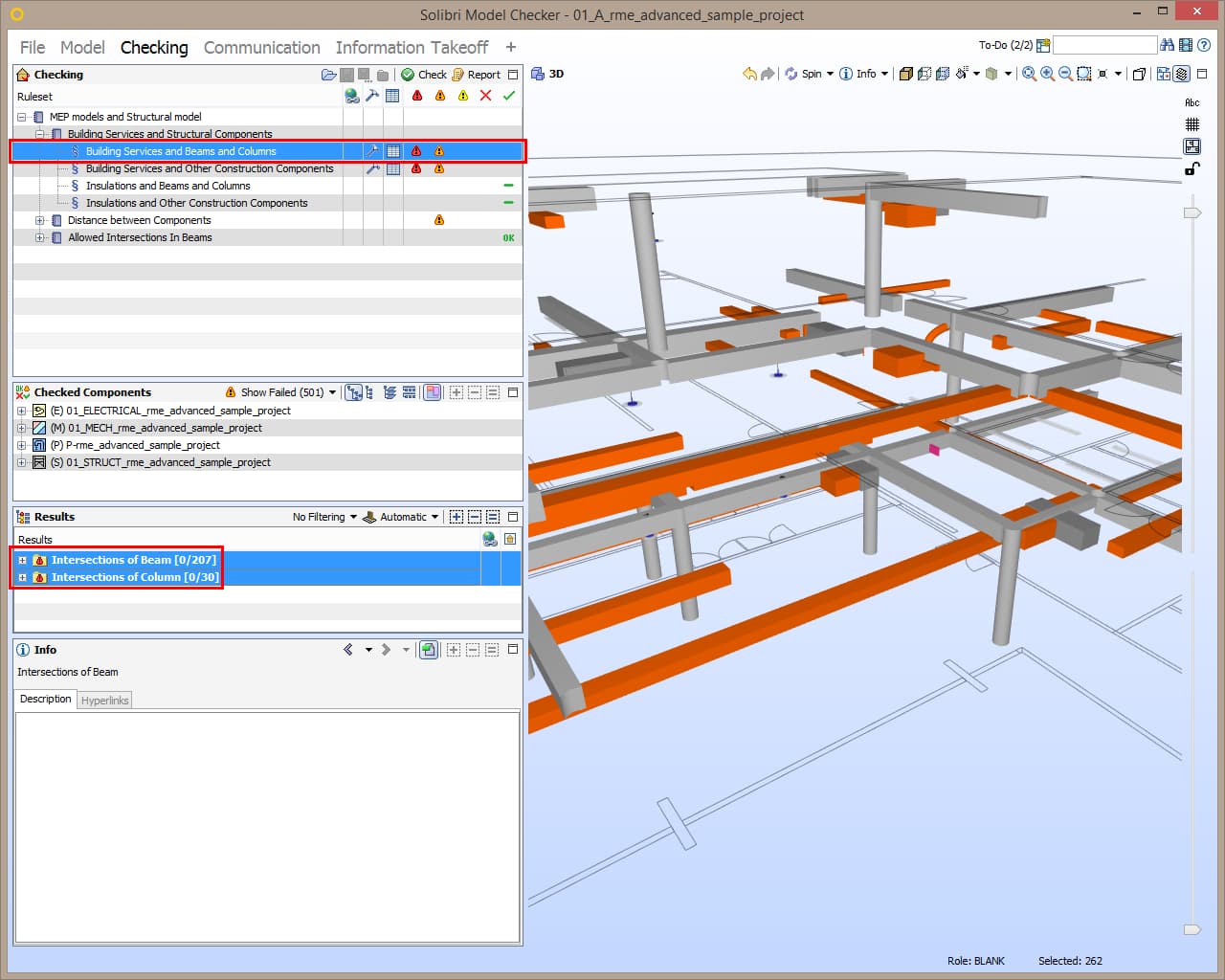
Problems It Solves
- Clashes Between Systems
Overlapping systems like ducts, pipes, and conduits can disrupt construction and require rework. Solibri eliminates these conflicts before installation begins.
- Code Compliance
Designs often fail to meet local or international building standards, risking legal issues or project shutdowns. Solibri validates compliance to prevent such outcomes.
- Delays and Rework
Late-stage detection of clashes or non-compliance can delay projects and escalate costs. Solibri catches these problems early, minimizing disruption.
Features and Unique Use Cases
- Advanced Clash Detection
- Solibri scans BIM models to identify conflicts between MEP systems, such as overlapping pipes and ducts, and flags these for resolution.
- Code Compliance Validation
- The tool comes with preconfigured rulesets that check designs against building codes, ensuring compliance with local and international standards.
- Users can also customize these rulesets to meet specific project requirements.
- Detailed Reporting
- Generates comprehensive reports highlighting detected issues, including their location and severity.
- These reports are actionable, enabling teams to address problems before they impact the construction schedule.
- Collaboration Integration
- Solibri integrates with leading BIM tools like Revit and Navisworks, allowing teams to share models and resolve clashes in a collaborative environment.
Step 4: Automating Fabrication
Tool: Stratus
Read more on their website here
Once the design is finalized and clashes are resolved, the next critical step is preparing for fabrication. This stage requires precision, especially in MEP systems where spooling, labeling, and tracking materials can be a logistical challenge. Stratus simplifies and automates these tasks, converting BIM data into fabrication-ready outputs. The result? A streamlined workflow that saves time, reduces errors, and keeps projects moving forward efficiently.
Stratus is a fabrication-focused tool that bridges the gap between design and installation. By automating the creation of spools, labels, and progress updates, it ensures every component is accurately tracked from the design phase to on-site execution.
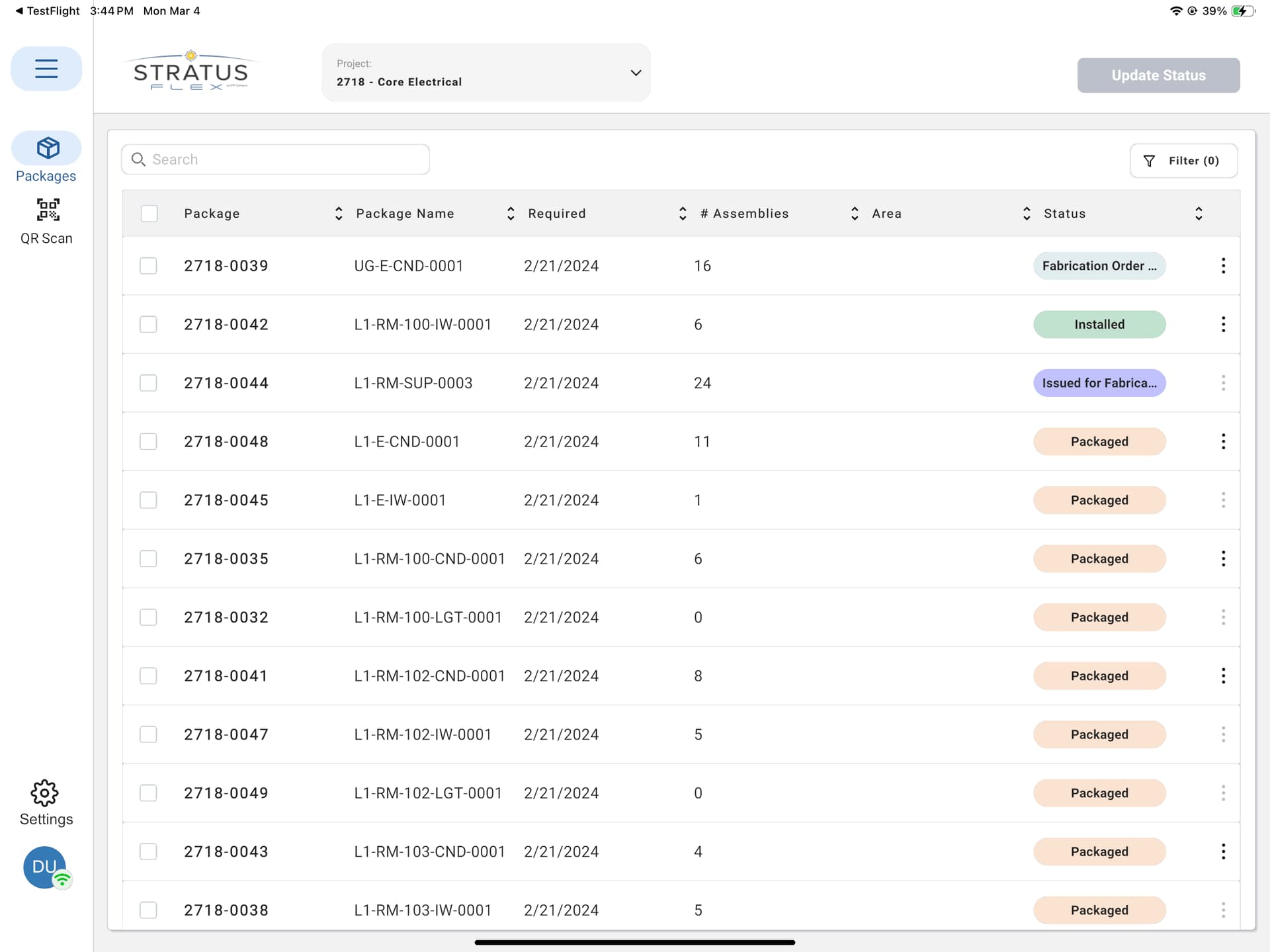
Problems It Solves
- Manual Errors in Fabrication
Human errors in spool creation or material tracking can lead to wasted resources and costly delays. Stratus minimizes these risks through automation. - Time-Consuming Processes
Manually generating spools, creating labels, and tracking materials is labor-intensive. Stratus reduces this workload significantly. - Lack of Visibility
Difficulty in tracking fabrication progress often results in delays. Stratus offers real-time updates, ensuring stakeholders stay informed.
Features and Unique Use Cases
- Automated Spooling
- Converts BIM data into detailed, fabrication-ready spools.
- Enables precise planning and assembly, reducing material waste and rework.
- Smart Labeling
- Automatically generates labels for components, ensuring accurate tracking from fabrication to installation.
- Labels are integrated with BIM data for seamless coordination.
- Real-Time Progress Updates
- Provides live updates on fabrication status, helping teams identify and address bottlenecks.
- Facilitates better communication between the shop and the field.
- Seamless Integration with BIM Tools
- Works alongside platforms like Revit to ensure continuity and accuracy from design to fabrication.
- Ensures all stakeholders operate from a unified data source.
Step 5: Monitoring Construction Progress in Real-Time
Tool: OpenSpace
Read more on their website here
Fabrication is only one part of the equation; keeping track of on-site progress is equally vital. Large MEP projects often involve sprawling sites with multiple teams working simultaneously, making it hard to monitor progress or spot issues. OpenSpace uses AI and 360-degree cameras to create a “digital twin” of your construction site, providing real-time visibility to stakeholders anywhere in the world.
OpenSpace combines advanced AI with simple tools like 360-degree cameras to document and monitor construction sites.
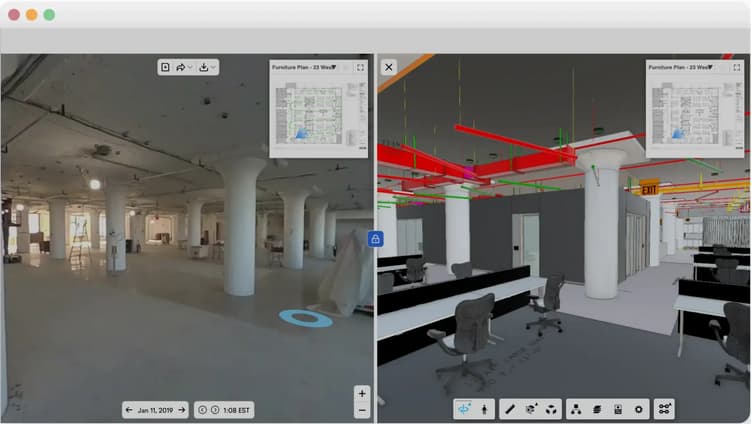
Problems It Solves
- Time-Consuming Documentation
Manual site reports are not only time-intensive but also prone to inaccuracies. OpenSpace automates this process, saving hours of work. - Limited Visibility for Stakeholders
Stakeholders who aren’t on-site often struggle to stay updated. OpenSpace provides them with real-time visuals and data. - Missed Issues
Without consistent monitoring, minor issues can snowball into costly problems. OpenSpace helps catch these early with precise, visual records.
Features and Unique Use Cases
- AI-Powered Vision Engine
- Automatically maps 360-degree images to floor plans, creating an accurate record of site conditions.
- Makes it easy to track progress and identify deviations from plans.
- 360-Degree Documentation
- Captures the entire site with a single camera pass, eliminating blind spots.
- Provides comprehensive records for progress updates and future reference.
- Remote Monitoring
- Allows stakeholders to access the site virtually, reducing the need for physical visits.
- Supports remote inspections, saving time and travel costs.
Step 6: Optimizing for Long-Term Efficiency and Maintenance
Tool: Hypar
Read more on their website here
As construction wraps up, the focus shifts to ensuring that MEP systems are not only optimized for immediate performance but also sustainable and efficient in the long term. With contractors increasingly looking to maintenance as a new revenue stream, tools like Hypar become invaluable. Hypar’s AI-driven generative design platform enables the creation of efficient MEP layouts while also helping contractors plan maintenance systems that can reduce costs and improve system longevity.
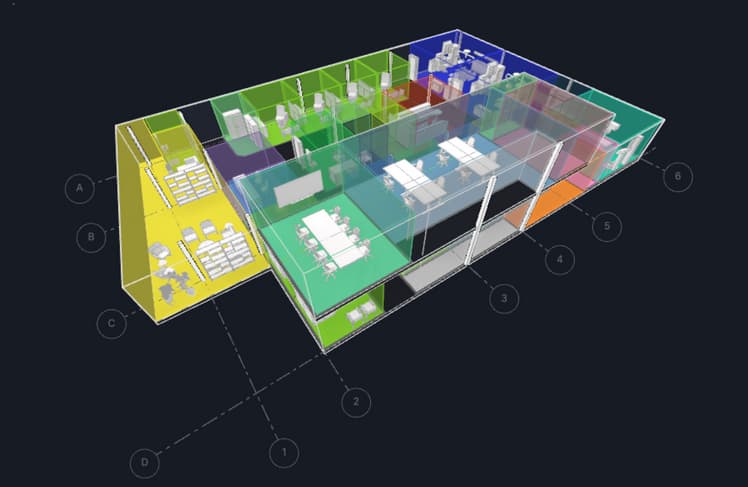
How Hypar Solves Key Problems
- Inefficient Layouts:
Suboptimal MEP designs can lead to increased energy consumption and higher operating costs. - Limited Maintenance Planning:
Traditional methods often overlook opportunities to incorporate efficient maintenance systems into designs. - Time Constraints:
Late-stage design adjustments are costly and time-intensive. - Sustainability Gaps:
Lack of focus on long-term environmental impact.
Key Features
- Generative Design
Hypar uses AI to automatically generate and analyze multiple layout options for MEP systems. This ensures optimal designs that balance cost, performance, and sustainability. - Data Integration for Smarter Designs
Incorporates real-world data like climate conditions, material costs, and building codes, allowing for contextually optimized layouts. - Customizable Maintenance Systems
Enables contractors to design and implement their own AI-driven maintenance systems by integrating IoT sensors and predictive analytics. This is a game-changer for contractors aiming to expand their services into maintenance. - Open-Source Flexibility
Hypar’s open-source platform allows users to create custom workflows tailored to unique project needs, including maintenance planning and operational efficiency.
Maintenance as a Revenue Stream
One of Hypar’s standout features is its ability to integrate maintenance planning into the design phase. Contractors can now use AI-powered insights to set up predictive maintenance systems. By embedding IoT sensors and automating alerts for system inspections or replacements, contractors can offer ongoing maintenance services to their clients, ensuring long-term relationships and creating additional revenue streams.
Facing Challenges, Finding Solutions
Adopting AI and automation in MEP workflows can feel overwhelming. With so many tools promising to transform your processes, it’s natural to wonder: Where do we begin?
You might be evaluating which tools align with your workflows, considering how to prepare your team, or thinking about integrating new technologies without disrupting ongoing projects. These are valid concerns—but they’re also opportunities to rethink how you work.
By focusing on selecting the right tools, empowering your team, and aligning technology with your processes, you can turn these challenges into meaningful progress.
At NeevIQ, we’ve seen these scenarios play out across the MEP and construction industries. While every project is unique, the key is always the same: starting with clarity. Identifying your needs, enabling your team, and integrating tools seamlessly into your workflow is the foundation for long-term success.
Learn more here
The tools in this blog are just the beginning. What truly matters is how you use them to fit your goals, team, and processes. If you’re ready to take the next step, we’re here to help you explore the possibilities.
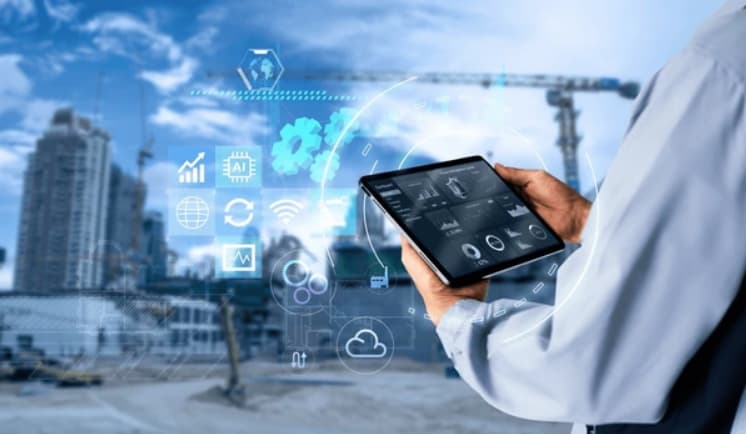
Conclusion: Balancing Innovation and Responsibility
AI is transforming MEP workflows by improving collaboration, reducing errors, and driving sustainability. But true progress comes from understanding and applying these tools effectively.
While AI optimizes designs and detects issues, expertise and judgment are essential for ensuring safety and structural integrity. Training teams and adopting these tools responsibly are critical steps forward.
As we embrace AI, robust checks and balances are vital. Final accountability always rests with us. By balancing innovation with responsibility, we can build smarter, safer, and more reliable systems for the future.